Introduction
In industrial and automotive pneumatic systems, valve reliability is non-negotiable. The WPS-CA/TG76 and WPS-CA/EP76 valves are critical components in applications ranging from process control to heavy machinery. Over time, wear and tear on diaphragms can compromise efficiency, leading to leaks, pressure drops, or system failures. Watson Diaphragm Kits provide a targeted, cost-effective solution to restore these valves to peak performance. Designed for precision compatibility and durability, these kits are engineered to meet OEM specifications, ensuring seamless integration and extended service life.
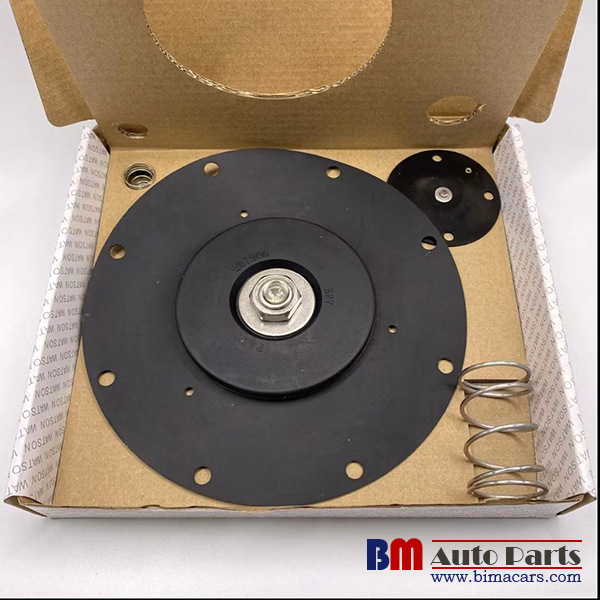
Why Diaphragm Integrity Matters in Pneumatic Systems
Diaphragms serve as the dynamic barrier between fluid or gas pathways in valves. In high-cycle applications, materials degrade due to repetitive flexing, temperature fluctuations, or chemical exposure. A compromised diaphragm can result in:
- Loss of Pressure Control: Reduced system responsiveness.
- Contamination Risks: Particulate ingress damaging downstream components.
- Increased Downtime: Unplanned maintenance halting operations.
Watson Diaphragm Kits address these challenges by using advanced elastomers like EPDM or fluorocarbon (FKM), selected for their resistance to abrasion, oils, and extreme temperatures (-40°C to 150°C).
Key Features of Watson Diaphragm Kits
- OEM-Equivalent Design
Each kit includes pre-molded diaphragms, seals, and fasteners tailored to the exact dimensions of WPS-CA/TG76 and WPS-CA/EP76 valves. This eliminates compatibility issues and ensures leak-free operation post-installation. - Material Innovation
Watson employs multi-layer reinforcement in diaphragms, combining flexibility with tear resistance. For corrosive environments, FKM variants offer superior chemical stability compared to standard nitrile rubber. - Comprehensive Kitting
Beyond diaphragms, kits include complementary components like O-rings, gaskets, and stainless steel springs—pre-assembled to streamline maintenance workflows. - Cost-Efficiency
Proactive diaphragm replacement reduces the risk of catastrophic valve failure, cutting long-term repair costs by up to 60% compared to full valve replacements.
Industry Applications
Watson repair kits are trusted across sectors demanding precision:
- Manufacturing: Ensuring consistent actuator performance in automated assembly lines.
- Oil & Gas: Withstanding hydrocarbon exposure in control valves.
- Transportation: Maintaining brake system valves in commercial vehicles.
Installation Best Practices
- Diagnose Early: Monitor valves for hissing noises or sluggish response—early signs of diaphragm wear.
- Clean Thoroughly: Degrease valve chambers to prevent debris interference.
- Torque Specifications: Follow manufacturer guidelines when tightening fasteners to avoid over-compression.
- Pressure Testing: Conduct a post-installation leak test at 1.5x operating pressure.
The Future of Valve Maintenance: Predictive Strategies
With Industry 4.0 driving smarter maintenance protocols, Watson kits align with predictive analytics trends. By integrating diaphragm replacement into scheduled upkeep cycles, facilities minimize unplanned downtime. Additionally, Watson’s QR-coded packaging enables quick access to installation guides and batch traceability.
Conclusion
Watson Diaphragm Kits represent more than a repair solution—they are a strategic investment in system reliability. By restoring WPS-CA/TG76 and WPS-CA/EP76 valves to OEM standards, operators safeguard productivity while reducing lifecycle costs.
For engineers and maintenance managers, adopting Watson kits translates to fewer emergencies, optimized performance, and compliance with stringent industry regulations.
More info about Watson Diaphragm Kits or diaphragm repair solutions, please visit our official website: www.bimacars.com.