Introduction
In industries where airborne particulates pose operational and safety risks—from cement production to pharmaceutical manufacturing—pulse jet valves are the unsung heroes of dust collection systems. The ASCO G353A046 Pulse Jet Valve stands at the forefront of this technology, delivering precise control and rugged durability. This article examines its engineering principles, industry applications, and maintenance strategies, equipping facility managers and engineers with actionable insights to optimize filtration performance.
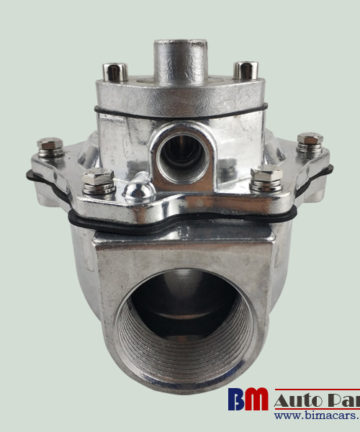
The Critical Role of Pulse Jet Valves in Dust Collection
Pulse jet valves regulate compressed air bursts to clean filter media, preventing pressure drop and maintaining airflow efficiency. A poorly functioning valve can lead to:
- Reduced filtration capacity
- Increased energy consumption
- Premature filter wear
The ASCO G353A046 addresses these challenges through:
- Rapid Response Times: 15 ms opening/closing cycles for consistent cleaning.
- High Flow Dynamics: 1.5″ orifice diameter optimized for large-baghouse systems.
- Robust Construction: Aluminum alloy body with PTFE seals resistant to moisture and abrasives.
Transition: Let’s delve into the technical specifications that make this valve a benchmark in industrial filtration.
Engineering Breakthroughs in the ASCO G353A046
- Coil Optimization
A high-efficiency solenoid coil (Class H insulation) ensures reliable operation at voltages from 24V DC to 120V AC, reducing downtime in unstable power environments. - Thermal Management
Engineered heat dissipation channels allow continuous operation at ambient temperatures up to 55°C—critical for foundries and kiln applications. - Sealing Innovations
Dual-layer PTFE diaphragms withstand 1 million+ cycles (per ISO 5599-1 testing), even in environments with oil aerosols or silica dust. - Smart System Integration
Compatibility with PLC-controlled timing boards enables adaptive cleaning cycles based on differential pressure sensors.
Transition: With its robust design, the G353A046 excels in diverse industrial scenarios.
Industry Applications & Performance Case Studies
- Cement Production: Handles limestone dust loads up to 500 g/m³, maintaining 99.97% filtration efficiency in vertical roller mill baghouses.
- Food Processing: USDA-compliant materials prevent contamination in flour silo venting systems.
- Waste-to-Energy Plants: Resists acidic flue gas condensates (pH 2–3) in electrostatic precipitator cleaning.
A 2023 retrofit project at a Canadian lumber mill demonstrated a 41% reduction in compressed air usage after replacing legacy valves with G353A046 units, achieving ROI within 7 months.
Maintenance Best Practices & Troubleshooting
- Preventive Measures
- Monthly diaphragm inspections for micro-cracks using UV dye tests.
- Annual coil resistance checks (target: 25Ω ±10%).
- Common Failure Modes
- Delayed Activation: Often caused by voltage drop—verify wiring gauge and controller output.
- Incomplete Pulse: Check for obstructed nozzles or undersized air receivers.
- Retrofitting Tips
When upgrading older systems, pair the G353A046 with ASCO’s ½” quick-exhaust valves to optimize pressure recovery times.
Transition: Proper maintenance transforms this component from a consumable into a long-term asset.
Conclusion
The ASCO G353A046 Pulse Jet Valve exemplifies how precision engineering can solve industrial pain points—reducing energy costs, extending filter life, and ensuring regulatory compliance. As dust emission standards tighten globally (e.g., EPA’s 2024 NESHAP revisions), adopting high-performance valves becomes both an operational necessity and a strategic advantage.
More info about ASCO G353A046 Pulse Jet Valves or diaphragm kits, please visit our official website: www.bmpneumatics.com.